SMTL Blog
- Details
Announcement: SMTL are now offering testing of disposable pulp products to BSI PAS 29
SMTL are pleased to announce the availability of a new test method for pulp products used in healthcare, to BSI "Product Assessment Specification PAS 29:1999 Disposable pulp products for use in healthcare".
Please contact SMTL as below if you want a quote.
Tel: +44 (0) 1656 752820
Email: physical@smtl.co.uk
- Details
Dr James Evans, one of SMTL's health services researchers, has recently had a paper published in Applied Health Economics and Health Policy ("Thopaz+ Portable Digital System for Managing Chest Drains: A NICE Medical Technology Guidance", Evans, J.M., Ray, A., Dale, M. et al. Appl Health Econ Health Policy (2019)).
The work, undertaken when James was working for CEDAR, assessed the clinical evidence for Thopaz+, and showed shorter drainage times and length of hospital stay, lower rates of chest drain re-insertion and higher rates of patient satisfaction when used in patients following pulmonary resection compared to conventional chest drainage. One comparative study of the use of Thopaz+ in patients with spontaneous pneumothorax was identified and showed shorter drainage times and length of hospital stay compared to conventional drainage.
The authors concluded that the use of Thopaz+ in patients following pulmonary resection and patients with pneumothorax led to cost savings compared to conventional drainage. The main driver for cost savings was a reduction in length of hospital stay.
- Details
Pete Phillips and James Evans were invited to the 9th RCSEd All Wales Medical & Dental Student Surgical Research symposium at Margam Orangery in October 2018 to judge poster and oral presentations and to present the SMTL award for best science paper.
The winner was Jeremy Chan and his colleagues Ren Chet Teh, Jacky Cheng, Pushpinder Sidhu for their poster on "Inappropriate blood tests in cardiac surgery intensive care".
Jeremy and his colleagues demonstrated that £75,000 could be saved in a single CSICU by eliminating unnecessary blood tests, and reducing the risk of anaemia due to iatrogenic blood loss. The poster exhibited three clear aims, a methodology which could be replicated, simple reporting of the results, good discussion of their limitations and a concise set of conclusions.
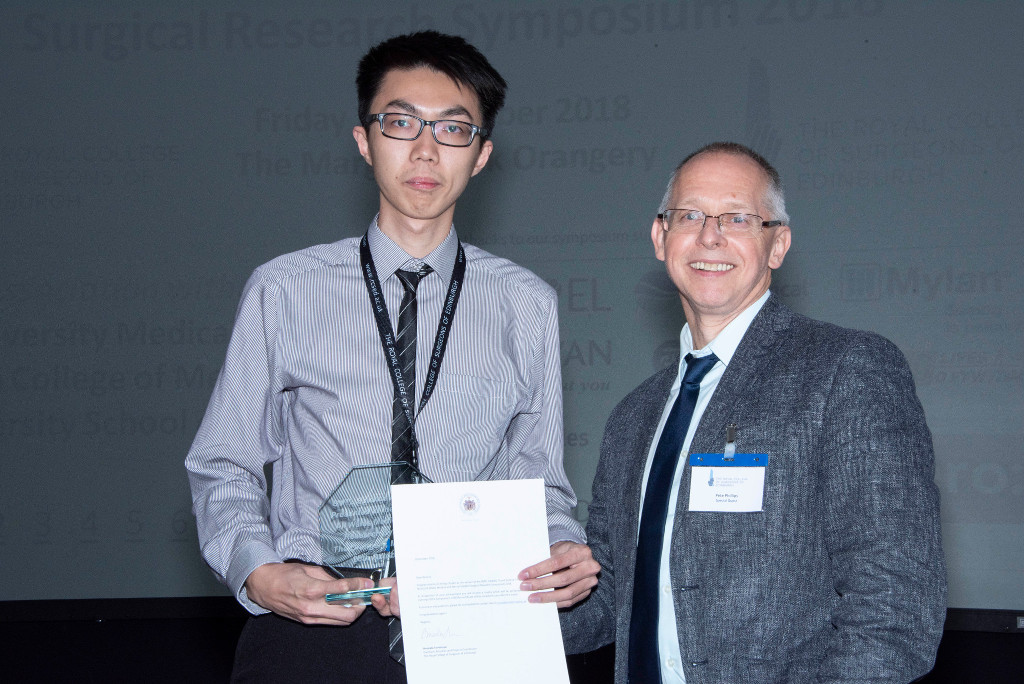
The photo shows Pete Phillips, Director of SMTL, handing Jeremy his award trophy
- Details
Since the first British Standards for compression hosiery were published in the 1980's, the use of compression garments to treat various clinical complications has changed significantly. Performance requirements and test parameters which seemed appropriate 33 years ago are now causing confusion for users of the products and operational difficulties for test houses and manufacturers.
To address these issues a new standard - BS 661210:2018 - has recently been published. BS 661210 is a revision and merger of three previous standards (BS 6612:1985, BS 7563:1999 and BS 7672:1993) for graduated compression hosiery, anti-embolism hosiery and graduated support hosiery. The BSI Panel took the opportunity of the revision to address inconsistencies in the previous standards, clarifying various test parameters and technical issues, and producing a single consistent test method to test both medical and non-medical compression garments.
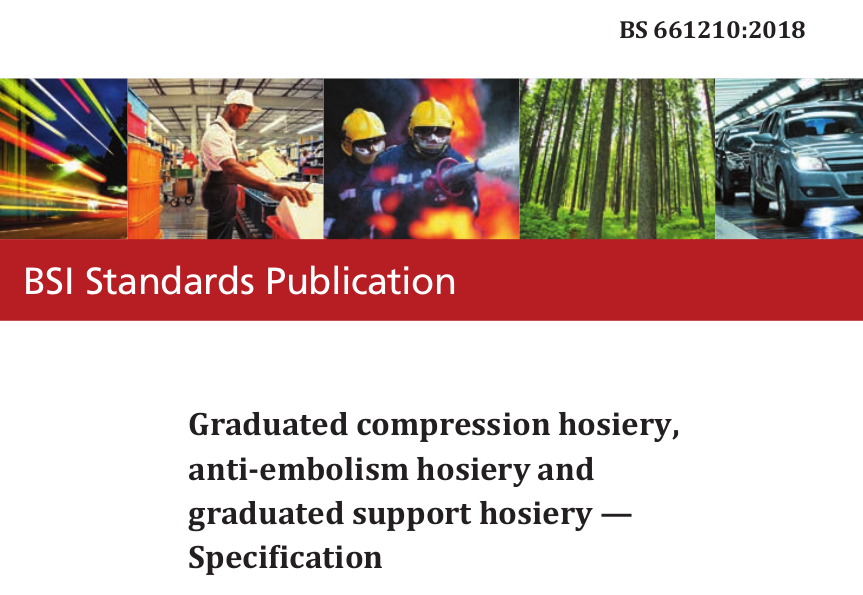
As well as specifying the test method, the Standard sets out performance requirements for the compression and stiffness of these devices, and these have been updated to reflect current clinical UK guidance . A new informative Rationale Annex (Annex C) has been included to explain the thinking behind most of the major changes in the Standard, and another new Annex (Annex D) explains the variety of classes and compression profiles used in the UK that are referenced in various standards and clinical guidance documents.
Peter Phillips (Director of SMTL) is chair of BSI committee CH/205/1, under which the Panel operated, and Dr Gavin Hughes (Deputy Director, SMTL) acted as Editor of the standard.
- Details